Buduję z głową
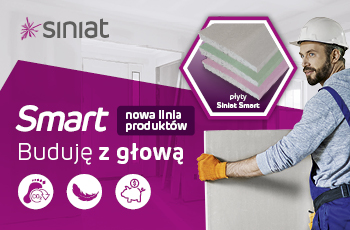
Ekipa Remontowa Siniat postanowiła zrobić sobie chwilę przerwy i zabrać widzów na wycieczkę. I to nie byle jaką – panowie zdecydowali się uchylić rąbka tajemnicy, jeśli chodzi o powstawanie produktów Siniat. W tym celu odwiedzili fabrykę ETEX Poland w Leszczach i pokazali nam, jak powstają słynne płyty gipsowo kartonowe.
Bezpieczeństwo w zakładach produkcyjnych to podstawa. Na teren fabryki nie można wejść bez odpowiednich zabezpieczeń. Na zestaw bezpieczeństwa składa się obuwie ochronne, kamizelka odblaskowa, kask oraz okulary ochronne. Gdy Ekipa Remontowa przywdziała wszystkie potrzebne elementy „garderoby”, fabryka stała przed nimi otworem.
Zwiedzanie zaczynamy jednak… na zewnątrz. Panowie pokazali nam imponujący taśmociąg, który dociera do zakładu prosto z kopalni. To on odpowiada za transport surowców potrzebnych do produkcji. Urobek z kopalni wędruje bezpośrednio do fabryki, a tam przetwarzany jest w płyty. Ale nie tak od razu…
Jest jeszcze inny taśmociąg, który nie dostarcza do zakładu urobku, a materiały z recyklingu, które są wykorzystywane do produkcji płyt. Czym są te materiały? Chodzi o pozyskiwany z elektrociepłowni gips syntetyczny oraz poprodukcyjne pozostałości płyt gipsowo-kartonowych. Oba taśmociągi łączą się w jednym miejscu, by dostarczać mieszaninę gotowego materiału.
Tuż za taśmociągami rozpościera się ogromny obszar do wykonywania kalcynacji gipsu – czyli procesu zamiany gipsu wodnego w gips półwodny. W tym miejscu możemy zauważyć mnóstwo różnego rodzaju młynów, suszarni, filtrów… Jest tego naprawdę sporo!
Płyty gipsowo-kartonowe składają się również z papieru, który znajduje się z obu stron płyty, trzymając całość w ryzach. To wyjątkowo gruby papier, składowany jest w magazynie w formie ogromnych beli. Jedna bela waży aż 3 tony i ma 14 kilometrów długości, a starcza jedynie na… 2 godziny produkcji. Papier ten posiada różne kolory, dobierane w zależności od rodzaju płyty, jaka ma być wytwarzana.
Tak ogromne rolki materiału nie mogą być obrabiane ręcznie. Służy do tego specjalny rozwijak. Jest on świetnie zautomatyzowany – po wykorzystaniu jednej beli ładuje od razu kolejną, tak aby nie było przestoju w produkcji.
Gips jest łączony z papierem – to czas formowania płyty! Ale zanim przejdziemy dalej, ta musi spędzić około 50 minut w suszarni. Po wysuszeniu, płyty lądują na dalszym etapie linii produkcyjnej, gdzie są automatycznie docinane i obrabiane na gotowy wymiar. Cały ten proces, jak i wiele innych w fabryce ETEX, jest zautomatyzowany. Czy wiecie, że podczas jednej zmiany na hali znajduje się jedynie 8 osób?
Przycięte płyty są składane, układane na paletach, a następnie wywożone na magazyn przez operatorów wózków widłowych. Czy to koniec? No nie. Każdy szanujący się producent sprawdza jakość swoich wyrobów. Zanim płyty trafią do dystrybucji, dział kontroli jakości bada je pod kątem zgodności z odpowiednią normą.
Proces ten musicie koniecznie zobaczyć w najnowszym odcinku Ekipy Remontowej – słowa nie oddadzą widoku tych wszystkich procesów. Jak podobała się Wam wycieczka z chłopakami z Siniat? Chcecie zobaczyć więcej zakulisowych materiałów i pomiędzy remontowymi wyzwaniami częściej wpadać na produkcję? Dajcie znać w komentarzach pod filmem i koniecznie subskrybujcie kanał, aby nie przegapić nowych odcinków.
Zobaczcie cały odcinek:
Podziel się z nami swoim projektem #SiniatPolska